“The Heart of Motion” describes the core of what we do and what we work for. That’s why it’s important to question the “heart” of motion and to take a fundamentally new approach to it. The anchor of an electromagnetic solenoid or the rotor of an electric motor are perhaps the most common, but not always the most ideal solutions for a job.
Magnetic fields lead to strains in magnetic shape memory alloys. This enables drives to be implemented where motion occurs on the interior of the material and tribological interfaces are avoided. We develop innovative drive concepts based on this effect under the name MAGNETOSHAPE®, from the material and actuator to the mechatronic system – always with the aim of creating the technologically best solution in line with our customers.
Magnetic shape memory technology explained briefly
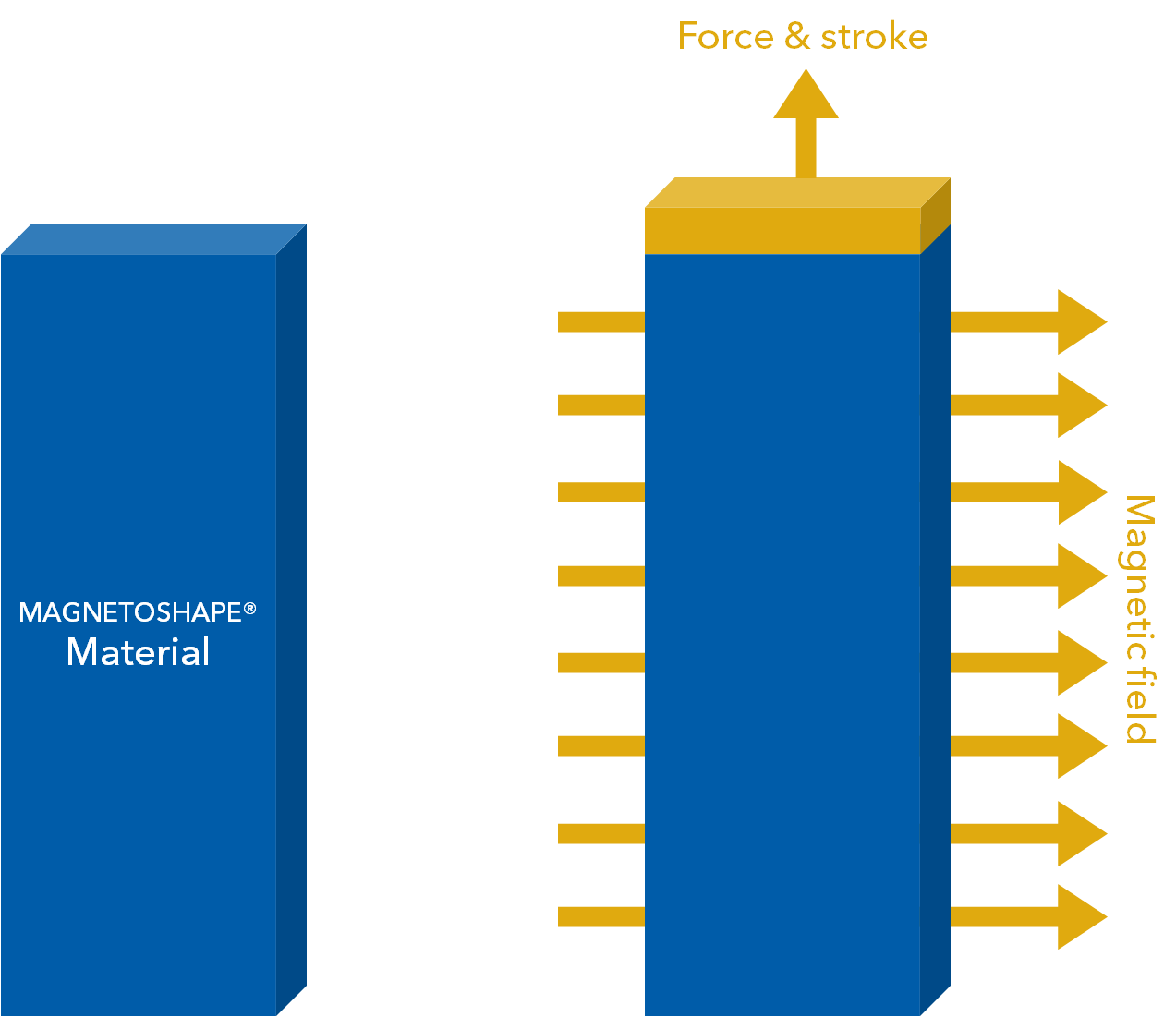
Magnetic shape memory alloys are ferromagnetic materials that generate force and motion under moderate magnetic fields. The typically single crystalline alloys made from nickel, manganese and gallium are able to generate 6% strain under external loads. And they do this with frequencies into the low kilohertz range.
The magnetic shape memory effect was discovered in the mid-1990s. Over the past few years, ETO has been carrying out intensive research in the area of the magnetic shape memory effect, significantly developing the material further and constructing actuators based on this. Today, ETO’s new MAGNETOSHAPE® is ready for use in initial series applications. Thanks to its unique advantages, the technology has the potential to replace electromagnetic and other actuator technologies in future.
Manufacture of single crystal MAGNETOSHAPE® material
· The raw materials are melted and alloyed inductively at around 1,400°C
· Large single crystals are drawn using a modified Bridgman process
· The crystals are heat-treated for chemical homogenisation and adjustment of the microstructure
· The crystal orientation is determined using X-ray diffraction
· The crystals are typically cut into cuboid elements
· The elements are configured for the application
Technical data of the MAGNETOSHAPE® material
MAGNETOSHAPE ® | |
Alloy | NiMnGa |
Field induced strain |
6 % under up to 2 N/mm² |
Blocking stress | Up to 3.5 N/mm² |
Switching field | 0.6 T |
Temperature limits | -40 °C – 60 °C |
High cycle fatigue | 2x109 (material) |
Typical element size | 1 x 3 x 10 mm³ to 6 x 6 x 30 mm³ |
Magnetic permeability | 2 (hard axis); 50 (easy axis) |
Frequency | DC to 1 kHz |
Switching speed | <1 ms (depending on actuator) |
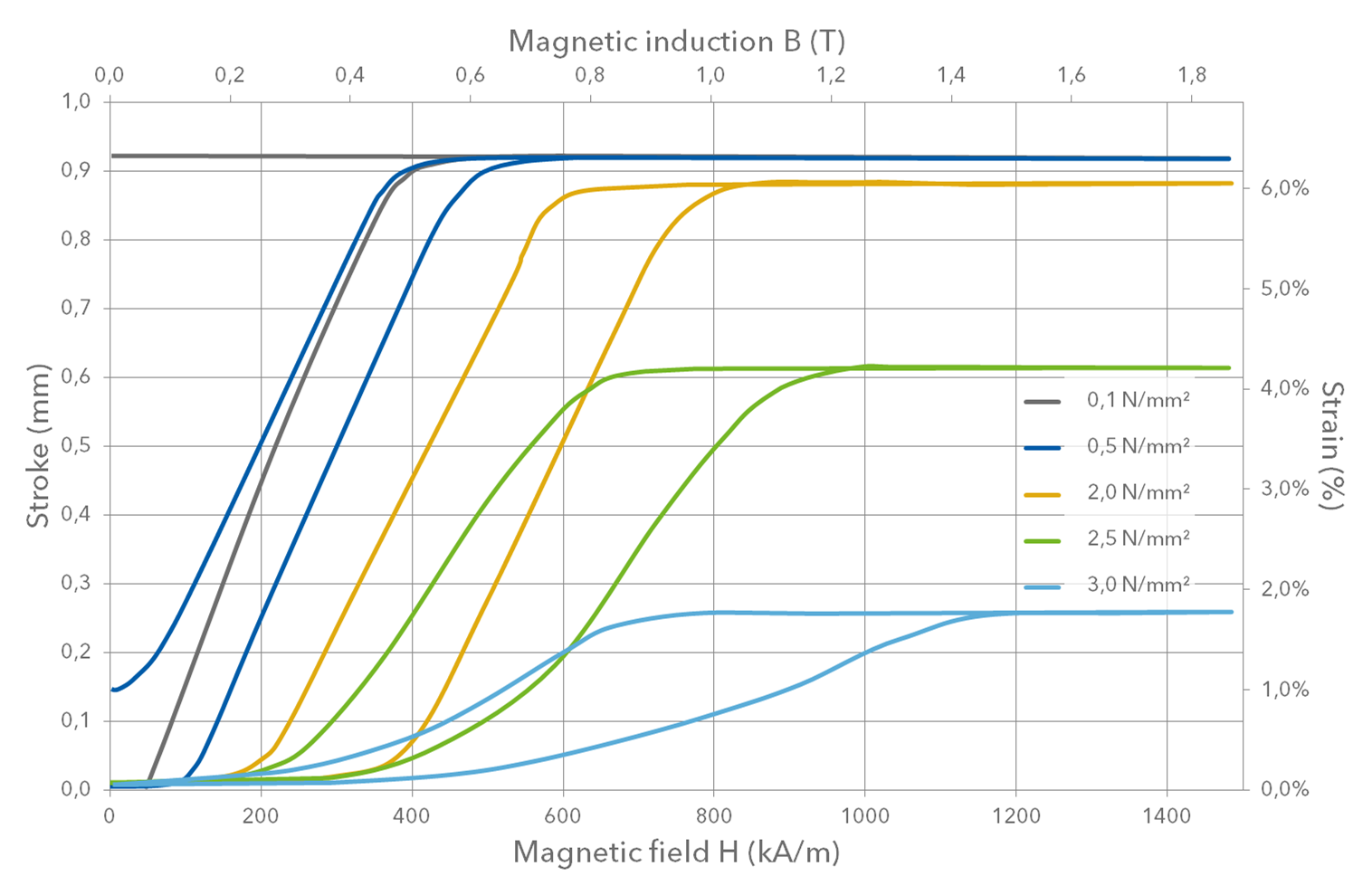
The design principles of the MAGNETOSHAPE® actuators
MAGNETOSHAPE® spring actuator
· Return springs opposite the MAGNETOSHAPE® element
· Extremely short switching times (~ 1 ms)
· Bistable variant with permanent magnet possible
· Different magnetic circuits dependent on the functionality needed (force, displacement, frequency)
MAGNETOSHAPE® push-push actuator
· Two MAGNETOSHAPE® actuator units work antagonistically
· Energy-efficient multi-stability
· Intermediate positions are stable without power consumption
· Enables fast and precise position control (< 5 µm)
Benefits of MAGNETOSHAPE® actuators
· Energy-efficient
· Offer a high work output at high frequencies
· Enable improved design of the actuator with low tribological wear
· Display extremely fast switching characteristics
· Allow for high service life applications
· Can be designed as bistable or multistable actuators as well as monostable actuators with fail-safe functionality
· Can be thermally activated simultaneously
· Offer self-sensing ability
Non-actuator applications
MAGNETOSHAPE® smart materials can also be used for non-actuator applications. This is enabled by the inverse magnetic and thermal shape memory alloy effect.
· Measurement of position, speed, force, pressure, etc.
· Energy harvesting for wireless energy supply
· Passive and active damping
· Use of specific alloys as high-temperature shape memory alloys (SMA)
· Thinned monocrystalline material (< 30 µm) for microsystem-based applications (actuator, sensor, harvesting)
· Thin-film materials are in development in academia
Publications
2015
· MSM-Greifer mit stationärer Aktuierung
2014
· Over 7% magnetic field-induced strain in a Ni-Mn-Ga five-layered martensite
· Magnetomechanical properties of a high-temperature Ni–Mn–Ga magnetic shape memory actuator material
· High-temperature magnetic shape memory actuation in a Ni–Mn–Ga single crystal
· FEM-Simulation of Magnetic Shape Memory Actuators
· Recent developments in magnetic shape memory actuation
· A modular energy efficient actuator based on magnetic shape memory alloys
· Magnetic Shape Memory Actuators for Fluidic Applications
2013
· Failure mechanisms and high-cycle fatigue of MSM actuators
2012
· Progress in developing smart magnetic materials for advanced actuator solutions
2011
· A Novel Concept for Strain Sensing Based on the Ferromagnetic Shape Memory Alloy NiMnGa
2010
Useful links